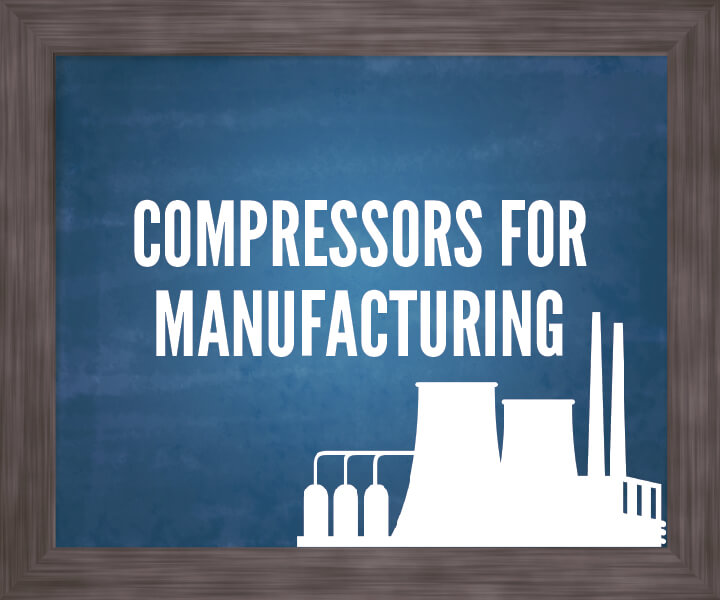
Compressors for Manufacturing
Most people give little thought to the important role of mechanical air compressors for manufacturing, residential, industrial, and agricultural applications in a modern society. For thousands of years, the human lungs functioned as a form of air compressors, which people used to stoke fires, but the carbon dioxide in human breath made it difficult to actually sustain fires. Plus, the practice of metallurgy — the melting down of metal such as copper and gold — required higher temperatures.
The need to develop a stronger method to produce compressed air rose dramatically and around 1,500 B.C., the invention of the bellows, a handheld device that consisted of a flexible bag, which generates a concentrated blast of air, made it possible to achieve higher temperature fires. The handheld bellow later gave way to a foot-controlled device.
German physicist Otto Von Guericke introduced a vacuum pump in 1650, which suctioned the gas from tight compartments and create air-free spaces. In 1762, professional engineer John Smeaton introduced a water wheel-driven blowing cylinder that gradually replaced the bellows. Around 1776, John Wilkinson invented the “blasting machine,” which became the first real archetype for modern-day mechanical air compressors.
By the 1800s, air compressors became more popular as more people began to take advantage of the ability to transmit energy. In 1888, Austrian engineer Viktor Popp invented the first mechanical air compression in Paris. In only three years, the capabilities of Popp’s compressor plant increased from 1,500 kilowatt (kW) to 18,000 kW. Applications for air compressors expanded from traditional metal working to the mining and fabrication of metals and ventilation for underground mining operations.
Over the years, companies involved in manufacturing air compressors have incorporated other features such as electricity and pneumatic energy into the devices. The use of air compressors to facilitate the movement of large volumes of air through the 8-mile-long tunnel constructed for the Italy-France rail system (1857) highlighted the numerous possibilities for the use of air compressors in the industrialized world.
In contemporary society, compressed air has found a place in nearly all fields of industry and commerce, including:
- Primary product industries (suppliers of semi-finished raw materials to manufacturers)
- Heavy goods manufacturers
- Consumer goods processing and packaging
- Transportation
- Construction
- Aerospace
- Automotive
- Cement production
A small shop may require a single compressor for manufacturing use, but a medium-sized company may have hundreds of uses for air compressors for manufacturing operations.
Air Compressors in Manufacturing Environments
Today, manufacturers rely heavily on modern innovations and mechanical systems to assist in a variety of operation processes. Industrial buildings, pumping systems, material handling, primary processing, and the maintenance and repair of various machinery and equipment create a high demand for compressed air. Many day-to-day processes in the manufacturing industry require the use of air compressors that can generate an intermittent or continuous source of pressurized air. In fact, similar to other entities, many companies in the manufacturing industry consider compressed air the “fourth utility” because it’s so important to production. It’s like water or electricity, and essential to operations.
Manufacturers understand the need for air compressors with the capacity or CFM rating to deliver a continuous or intermittent supply of durable, dependable, clean, and efficient pressurized air. The wide variety of primary and auxiliary manufacturing activities and applications that require compressed air include:
- General manufacturing – Clamping, stamping, tool powering and cleaning, controls and actuators
- Furniture manufacturing – Air piston powering, tool powering, clamping, spraying, controls and actuators
- Plastics, silicone and rubber manufacturing – Mold press powering, tool powering, clamping, and forming, injection molding
- Metal Fabrication – Assembly station powering, controls and actuators, injection molding, tool powering, and spraying
- Glass, Stone, Clay – Conveying, blending, mixing, controls and actuators, glassblowing and molding, cooling
- Mining – Hoists, pumps, pneumatic tools controls and actuators
- Food and Beverages – Dehydration, bottling, controls and actuators, conveying, spraying coatings, cleaning, vacuum packing
Quincy Compressor provides viable solutions to manufacturers with a need for a mechanical system to move power around their facilities.
Hear From Our Customers
Types of Air Compressors
Air compressors are designed to pressurize air to a certain level and deliver it in a steady stream to drive tools, machines and processes. Most of today’s air compressors for manufacturing and other industrial uses come prepackaged with the compressor, drive motor and other accessories secured to a frame, which facilitates movement and installation. The size and configuration of the air compressor determines if it will work for the location and application. The most common type of air compressor is the positive displacement.
The positive-displacement air compressor has a specific quantity of air or gas trapped in a compression chamber. When the volume the gas or air occupies drops (mechanically reduced), it causes a corresponding rise in pressure prior to the discharge. The air flows from the compressor at a constant speed, which remains consistent with the changes in the discharge.
You can divide positive-displacement compressors into two categories: reciprocating and rotary:
- Rotary screw. This positive-displacement air compressor has a matching pair of helical screws that drives air into a special chamber. It simultaneously shrinks the size of the chamber, which compresses the air.
- Reciprocating/piston. In the positive-displacement compressor family, reciprocating compressors, which are available in single stage and two stage configurations, use a series of one-way valves to push air into the chambers. A series of pistons, operating in constant motion, compress the air. Single-stage air compressors draw air in and compress the air to its final pressure in a single piston stroke. Generally, single-stage pumps have a higher CFM rating compared to a two-stage pump because each cylinder draws in air and compresses it with every rotation.
Two-stage compressors process the air in two stages. After drawing the air in, the device compresses it to an intermediate level, pipes the semi-compressed air to another area in the compressor, and allows the air to cool before the final compression. Reciprocating air compressors for manufacturing applications can reach pressures up to 500 psig.
To maintain reciprocating and rotary screw compressors and keep valves and pistons moving, regular lubrication is required. However, some operations that use an air compressor for manufacturing, such as food and beverage companies and pharmaceutical companies, require Class Zero air quality. This means that the compressed air must be 100% oil-free in order to avoid even the smallest chance of contamination.
Oil-free air compressors such as the Quincy QOF 2-30 oil-free scroll compressors meet the requirement for operations in a clean environment. A combination of low maintenance, low operating costs, and outstanding reliability make oil-fee compressors a solid investment for operations that must meet the Class Zero cleanliness standard.
The third major category for air compressors consists of the centrifugal — the largest of the three types of air compressors. Powered by steam turbines or electric motors, centrifugal air compressors are primarily used in large industrial manufacturing processes that require a massive amount of air pressure. Centrifugal air compressors cost significantly more than their rotary screw and reciprocating counterparts. In addition, centrifugal units must receive constant maintenance and have significantly higher repair costs due to the high velocities and continuous use.
Choose a Rotary Screw or Reciprocating Compressor for Manufacturing Use
The line of Quincy air compressors for manufacturing use includes innovative rotary screw products such as the highly advanced QGV®️, a 20-200 hp variable speed model that offers the most stable air pressure of any compressor with an 85% turndown. In addition to the remarkably low cost of ownership, the QGV®️ is also extremely easy to operate and maintain.
Our manufacturing-use air compressors also include top-performing reciprocating units starting with our tough QTs, tougher QPs and our toughest QR-25 series. A QT air compressor provides more air while consuming less energy. These two-stage compressors also include a cast iron crankcase and cylinders as well as high-efficiency inner coolers. The one-piece aluminum head maximizes the compressors strength and also dissipates heat. The splash-lubrication models offer rugged reliability. Quincy’s innovative pressure-lubricated models offer extreme performance built to last for decades.
Not sure whether a reciprocating piston or rotary screw compressor is right for your needs? This great graphic will help make the decision easier:
Compare Air Compressors: Calculate the Total Cost of Ownership
Sourcing numerous air compressor models to find the right one for your manufacturing operations can overwhelm you rather quickly. The key is to determine the complete cost of ownership for the compressor you choose. When comparing the different options, consider the initial purchase cost as well as the operation costs over a five-year period. Use the following five-step process:
Step 1: Prior to obtaining a quote and/or ordering your compressor, calculate the voltage and phase requirements for the location where you will install the air compressor. For example, your voltage requirement for the location may be 230 volt – 3 phase.
Step 2: Calculate how much air will be required for your shop or application. Measure the volume of air in cubic feet per minute (CFM). The CFM determines how many tools you can run and how much power you need. Calculate CFM by adding the air requirement for each tool (used frequently) and divide by 35% — the utilization factor (UF). The UF means that the average shop uses one tool used 35% of the workday and provides a simplified method for determining your air demand.
For example, suppose you have the following tools in your shop: ¼-inch impact wrench – 8.0 CFM @ 125 PSI, 3/8 inch drill – 9.0 CFM@ 100 PSI, and small die grinder – 7.0 CFM@ 125 PSI. You would:
- Add 9.0 + 7.0 + 8.0 = 24 CFM
- Multiply 24 CFM x .35 (UF) = 8.4 CFM air demand
Step 3: Determine the air pressure needs for your shop or application. Look at the air pressure requirements for each tool. The tool with the highest air pressure requirement determines the minimum pressure. Generally, one stage compressors, which include rotary screw compressors, have a 125 PSIG maximum continuous pressure rating. The majority of two-stage compressors operate up to 175 PSIG, and they can be regulated down to lower pressures, which gives you the benefit of more air at a higher pressure in the tank.
Referring to our earlier example, both the die grinder and impact wrench require 125 PSI, which means that the compressor must have a minimum line pressure of 125 PSI. You could choose a single-stage compressor to operate these tools. However, because the single-stage compressor has a maximum output of 125 PSI, it makes more sense to consider a two-stage compressor that has a maximum output of 175 PSI. A two-stage compressor offers the following advantages:
- It stores more air in the same amount of space at a higher pressure, and it runs less often than a single-phase air compressor, which saves wear and tear on the unit and lowers operating costs.
- Two-stage compressors run cooler compared to a single-stage, which enhances reliability and prolongs the compressor life.
Review your requirements for a new air compressor and compare them to the specifications of the products under consideration. Most industries have a standard 75% duty cycle. This means that the compressor will operate 75% of the time and remain idle 25% of the time. Determine the amount of air the compressor will need to deliver in order to maintain the 75% duty cycle. Divide the estimated air demand by .75. Using the above example of 8.4 CFM /.75 equaling 11.2 CFM, you will need to purchase a compressor that delivers at least 11.2 CFM and has a minimum output pressure of 125 PSI.
Step 4: Verify with a certified electrician that you have the required electrical service to operate the compressor you intended to purchase. The information the electrician will require includes the full load amperage rating, which you can find on the electric motor nameplate, the voltage requirements, and the phase.
Step 5: To calculate the full cost of ownership, you must include expenses for the proper maintenance of the unit based on the manufacturer’s specifications. The costs typically include:
- Oil changes at predetermined intervals
- Valve replacement
- Replacement of air filter elements
- Replacement of oil separator elements (rotary screw air compressors only)
To control your operating costs, it is critical that you choose an air compressor with enough CFM to deliver the most air and that requires the lowest brake horsepower.
Key Factors for Selecting a Manufacturing Air Compressor
You can easily become overwhelmed with the numerous air compressors available in the marketplace. After you complete your due diligence and determine which air compressor is right for your shop or application, the next task is to figure out which model meets your need.
Keep in mind that not all air compressors are created equal. Here are some key considerations to incorporate into the decision-making process:
- Power: It is critical that you choose an air compressor that will drive tools and power your machines and processes so that you get the job done with no hassles.
- Efficiency: The more power an air compressor requires, the higher the fuel cost, which is a significant operating expense for many operations. Reduce your cost as well as your carbon footprint by choosing an air compressor that is energy efficient.
- Maintenance requirements: Similar to other industries, if your compressor breaks down, it has a negative effect on productivity and your bottom line. Choose a quality air compressor that requires as little maintenance as possible to ensure that your operations run smoothly and at optimal capacity.
- Warranty: Choose an air compressor manufacturer that stands behind their product with a strong warranty. Quincy Compressor offers one of the industry’s best warranties, which includes extended coverage for select models for up to 10 years on the core parts of the unit.
Air compressors are a significant investment for manufacturers and other businesses. It is important that you understand the factors that affect equipment performance before you purchase. As you weigh the options, evaluate the CFM requirement for your operations. You should also forecast future demands for your operation, which may require a larger air compressor. Backed by almost 100 years of experience providing air compressor solutions, we designed the QP as a mid-range, pressure-lubricated air compressor for manufacturing and other industries. The QP will provide you maximum productivity, efficiency and longevity for the most demanding 175 PSI applications and processes.
Contact a Quincy Compressor sales and service professional for assistance in identifying the best air compressor for your industrial operations. Learn more about the legendary performance and reliability of Quincy Compressors for manufacturing and other industries.
Recommended Products…
- QSI
- QGV®️
- QR-25
- QT (251CP80VCB, 251CS80VCB, 271CS80VCB, P2101CS12VCB, P2103DS12HCB, 2153DS12HCA, G213H30HCB, G214K30HCD)
- QP (351CS80VCB, 371CS80VCA, 3103DS12HCA, 353DS1HCA, G313H30HCE, G314K30HCE)
Case Studies
Here are two real-world examples of how installing Quincy compressors for manufacturing use has helped companies save energy and operate mraytheon-1108ore efficiently, while also minimizing ownership costs:
Experience the Legendary Quincy Compressor Performance and Reliability
Quincy Compressor has been in business for nearly 100 years. During this time, we’ve established an impeccable reputation as being among the leading air compressor manufacturers when it comes to performance and reliability. We also back our compressors with industry-leading extended warranty programs that do not require users to enter a service contract.
Contact Us to Learn More About Your Manufacturing Air Compressor Options
Learn more about our wide range of air compressors for manufacturing use by contacting us directly. You can also get in touch with the authorized Quincy Compressor dealer in your area with our sales and service locator.